Panelists: Moderator John Tylko, chief innovation officer, Aurora Flight Sciences; Fay Collier, project manager, Environmentally Responsible Aviation, NASA’s Langley Research Center; Mark Drela, Terry J. Kohler professor, Department of Aeronautics and Astronautics, Massachusetts Institute of Technology; Alan H. Epstein, vice president of technology and environment, Pratt & Whitney; Robert H. Liebeck, chief scientist of the blended wing body airplane program, Boeing Defense, Space & Security
by Hannah Godofsky, AIAA Communications
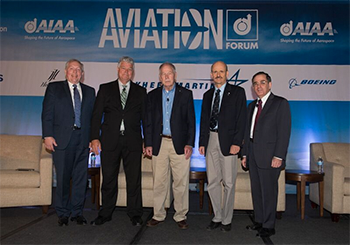
Flight has already become much more efficient over the past 60 years, but with further optimization as well as the implementation of new designs and new fuels, an even greener future is possible, according to members of the “Perspectives and Progress on Green Aviation” panel June 5 at the 2017 AIAA AVIATION Forum in Denver.
“The industry curve is largely flattened at roughly a 1.5 percent annual improvement, and no surprise the aircraft silhouette has remained largely the same since the introduction of the 707,” John Tylko, chief innovation officer at Aurora Flight Sciences, said of the status quo in fuel efficiency and green aviation.
Fay Collier, project manager of Environmentally Responsible Aviation with NASA’s Langley Research Center, said NASA has set bigger goals for reducing emissions and aircraft noise. He said NASA’s N+2 and N+3 goals aim to create new airframe and engine integration concepts to reduce noise and fuel burn.
One such example is the X-48B demonstrator. Robert Liebeck, chief scientist with the blended wing body airplane program at Boeing, said researchers at NASA’s Armstrong Flight Research Center have performed 122 test flights to date of the blended wing body aircraft.
“The airplane is robust and flies very well,” said Liebeck, showing a diagram of the structure of an X-48, which looks more like a cross-section of a submarine. “Structure … was the big challenge. You have bending loads in both directions, and then you’ve got a pressure load.”
Mark Drela, a professor at the Massachusetts Institute of Technology, spoke about design and optimization.
“Any time you have a new technology, there’s a very good chance — in fact, it’s almost certain — that the best use of that technology will be somewhere away from the current design practice,” Drela said. “We think it’s really important to re-optimize the entire system — and by system, I mean the airframe, the engine and the operation parameters — simultaneously so that you fully realize that potential of the new technology.”
Even if each optimization increases fuel efficiency by only 1 or 2 percent, he said, that could really add up across 20 different optimizable features.
Alan Epstein, vice president of technology and environment at Pratt & Whitney, explained that the propulsion system is currently about 20 percent of the value of a new airplane with today’s designs and that increasing that cost means gains in efficiency have to be substantial enough for airlines to be able to justify investment in a new system.
“At the current cost of fuel, the hybrid-electric airplane has to be 42 percent better in fuel burn to be cost neutral,” he said.
That’s a tough goal to meet, Epstein explained, adding that the math for new, more efficient aircraft does look better if fuel prices are higher.
“So how do we really go green?” he asked. “We go with sustainable alternative jet fuels. There’s hundreds of millions of gallons on order. If you fly out of LAX, now you’ll fly partially on sustainable alternative fuels.”
Videos
Part 1
Part 2